Laser cutting machines are revolutionizing manufacturing. Their precision and efficiency have made them essential tools. However, their true potential is realized when combined with smart manufacturing. This integration is driving innovation and improving production processes. In this article, we explore how laser cutting machines and smart manufacturing work together.
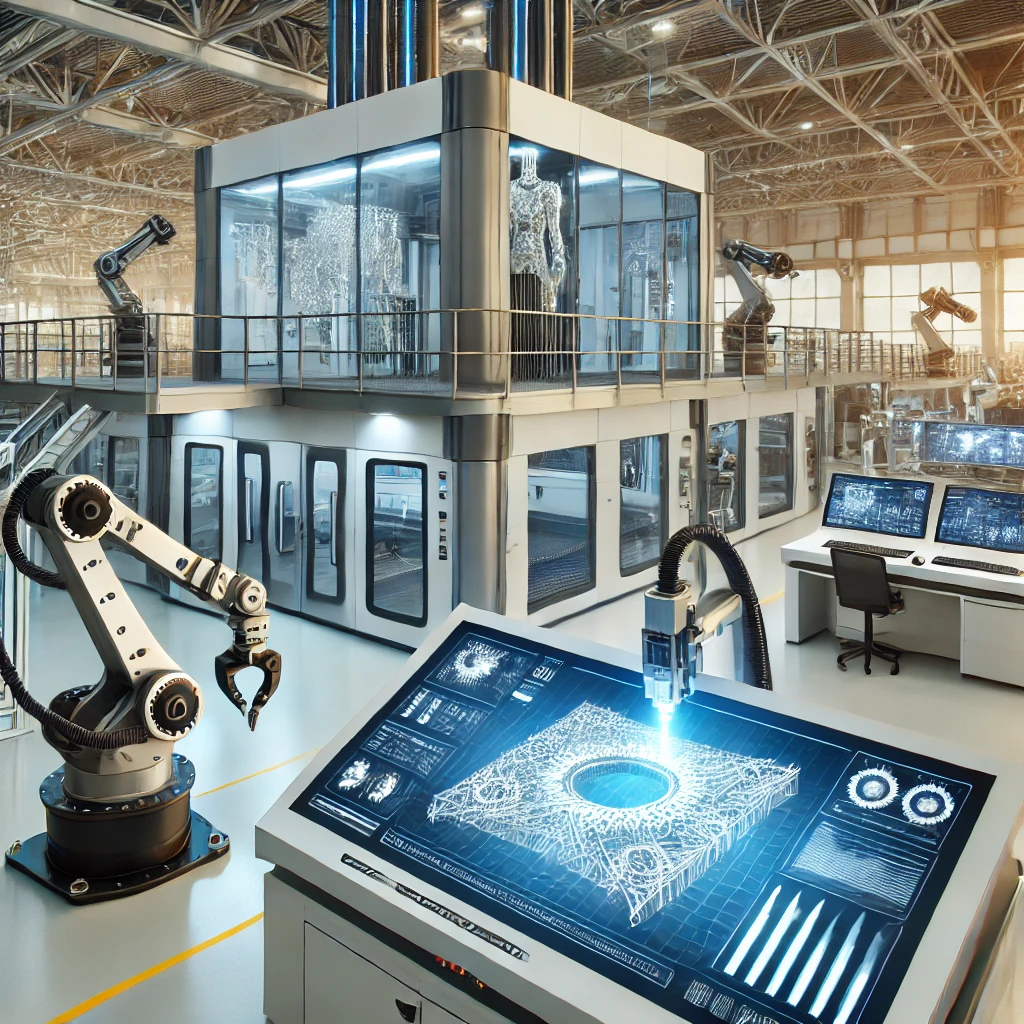
I. Enhancing Precision and Efficiency
Laser cutting machines are known for their precision. They can cut complex shapes with unmatched accuracy. However, smart manufacturing takes this to the next level. By integrating laser cutting machines with smart systems, manufacturers can enhance precision even further. These systems monitor and adjust cutting parameters in real-time. As a result, the machines consistently produce high-quality parts. Additionally, smart systems optimize cutting paths. This reduces material waste and increases efficiency. The combination of laser cutting and smart manufacturing delivers superior results.
II. Real-Time Data Collection and Analysis
Smart manufacturing relies heavily on data. Laser cutting machines equipped with sensors collect valuable data. This data includes information on machine performance, cutting accuracy, and material usage. Smart systems analyze this data in real-time. They identify trends, detect anomalies, and make adjustments as needed. For example, if a machine’s performance declines, the system alerts the operator. This proactive approach prevents downtime and ensures consistent production quality. Moreover, real-time data helps manufacturers make informed decisions. They can optimize processes based on accurate, up-to-date information.
III. Automation and Reduced Human Error
Automation is a key component of smart manufacturing. Integrating laser cutting machine with automated systems reduces the need for manual intervention. This, in turn, minimizes human error. Automated systems control the entire cutting process. They load materials, position them correctly, and start the cutting operation. Once the cutting is complete, automated conveyors move the finished parts to the next stage. This seamless process ensures consistency and reduces the likelihood of errors. Additionally, automation frees up human workers. They can focus on more complex tasks that require critical thinking.
IV. Improved Production Flexibility
Flexibility is crucial in modern manufacturing. Laser cutting machines, combined with smart manufacturing, offer unparalleled flexibility. Smart systems can quickly adapt to changes in production requirements. For example, they can switch between different cutting programs with ease. This allows manufacturers to produce a wide variety of parts without lengthy setup times. Additionally, smart systems can handle different materials without manual adjustments. This versatility is especially valuable in industries that require customized products. As a result, manufacturers can meet diverse customer demands efficiently.
V. Predictive Maintenance and Increased Uptime
Maintenance is essential for keeping laser cutting machines running smoothly. However, traditional maintenance schedules can be inefficient. They may result in unnecessary downtime or missed issues. Smart manufacturing addresses this problem with predictive maintenance. Sensors on the laser cutting machines continuously monitor their condition. The smart system analyzes this data and predicts when maintenance is needed. This approach prevents unexpected breakdowns. By scheduling maintenance only when necessary, manufacturers maximize machine uptime. Predictive maintenance also extends the lifespan of the machines. As a result, companies save money on repairs and replacements.
VI. Enhanced Quality Control
Quality control is a top priority in manufacturing. Laser cutting machines integrated with smart manufacturing ensure consistent quality. Smart systems monitor every aspect of the cutting process. They detect any deviations from the set parameters. If a problem occurs, the system can automatically adjust the settings or stop the operation. This real-time intervention prevents defective products from reaching the next stage. Additionally, smart systems maintain detailed records of each production run. This data is invaluable for quality assurance. It allows manufacturers to trace issues and implement corrective actions.
VII. Energy Efficiency and Sustainability
Energy efficiency is increasingly important in manufacturing. Laser cutting machines consume significant amounts of energy. However, smart manufacturing can reduce this impact. Smart systems optimize the machine’s energy usage during operation. They adjust power settings based on the material and cutting requirements. This ensures that the machine uses only the necessary amount of energy. Additionally, smart systems can schedule operations during off-peak hours. This reduces energy costs and minimizes the environmental impact. By combining laser cutting machines with smart manufacturing, companies can achieve their sustainability goals.
VIII. Scalability and Future-Proofing
Manufacturing needs change over time. Companies must be able to scale their operations. The integration of laser cutting machines with smart manufacturing offers scalability. Smart systems are designed to grow with the business. As production demands increase, the system can handle more machines and processes. Additionally, smart manufacturing is adaptable to new technologies. This future-proofing ensures that the investment in smart manufacturing continues to pay off. Companies can integrate new advancements without overhauling their entire system.
IX. Collaborative Robotics and Human-Machine Interaction
Collaborative robotics, or cobots, are becoming more common in manufacturing. These robots work alongside humans to perform tasks. When integrated with laser cutting machines, cobots enhance productivity. They can load and unload materials, position them accurately, and even assist in quality control. This collaboration between humans and machines improves efficiency. Moreover, smart systems facilitate smooth interaction between cobots and laser cutting machines. This ensures that both work in harmony, maximizing output.
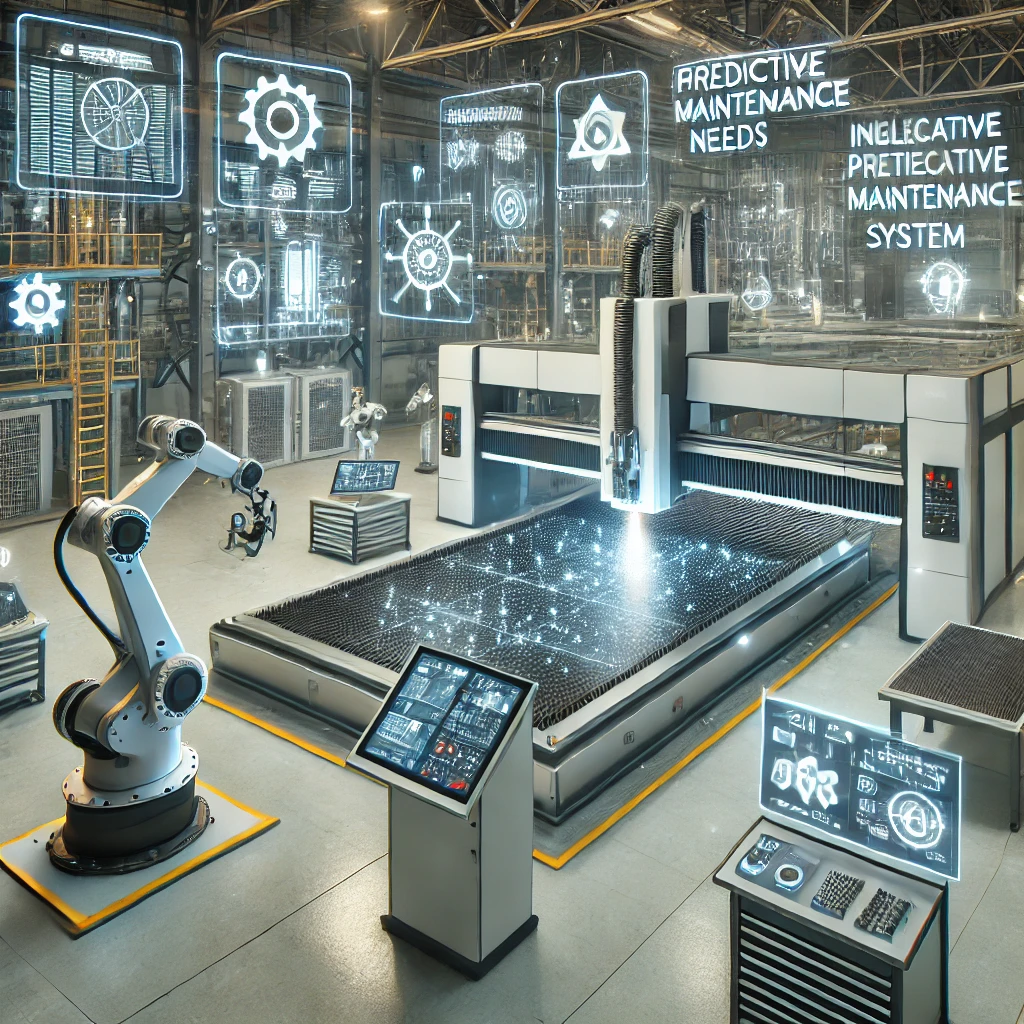
X. Conclusion
The integration of laser cutting machines with smart manufacturing is transforming the industry. It enhances precision, efficiency, and flexibility. Real-time data collection and analysis improve decision-making and reduce errors. Automation and predictive maintenance increase uptime and reduce costs. Moreover, this integration supports sustainability and scalability. As technology continues to evolve, laser cutting machines and smart manufacturing will lead the way. The future of manufacturing is smart, efficient, and highly adaptable. Companies that embrace this integration will stay ahead in a competitive market.