Laser cutting machines are invaluable tools in modern manufacturing and production processes, known for their precision, speed, and versatility. However, to maintain their efficiency and prolong their lifespan, proper care and maintenance are essential. We’ll explore various strategies and best practices to extend the operational life of a laser cutting machine, including regular maintenance, proper usage techniques, and the importance of maintaining optimal environmental conditions.
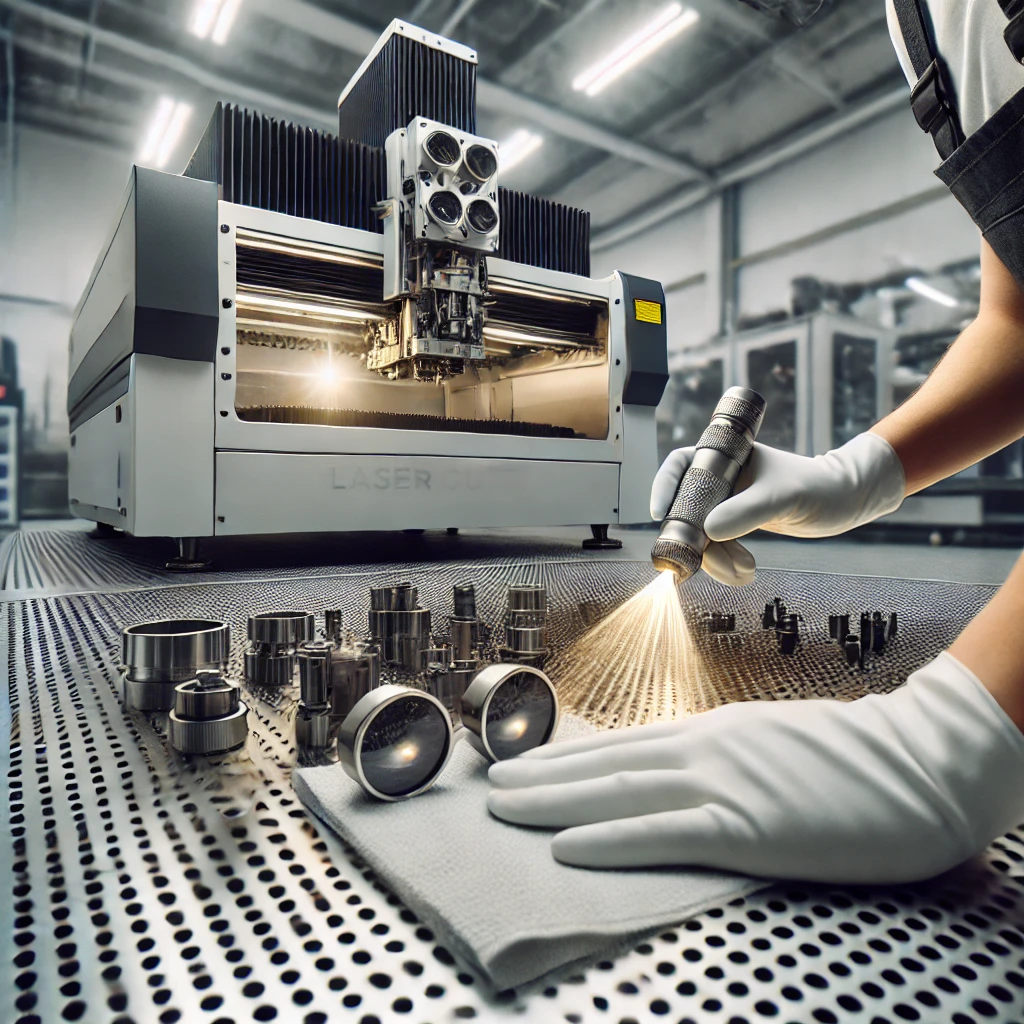
I. Regular Maintenance
Firstly, consistent and regular maintenance is crucial in extending the lifespan of a laser cutting machine. This involves a series of routine checks and servicing to ensure all components function optimally. Key maintenance activities include:
1. Cleaning Optics
The optics, including lenses and mirrors, are integral to the laser cutting process. Over time, these components can accumulate dust and debris, which can impair the laser beam’s quality and efficiency. Therefore, regular cleaning using appropriate materials and techniques is essential to maintain clear optics.
2. Checking and Replacing Consumables
Consumables such as nozzles, lenses, and filters wear out over time and require periodic replacement. Monitoring these components and replacing them when necessary prevents degradation in cutting performance and helps avoid potential damage to the machine.
3. Lubrication of Moving Parts
The moving parts of the machine, including rails, bearings, and gears, require proper lubrication to reduce friction and wear. Regularly applying suitable lubricants ensures smooth operation and prolongs the life of these mechanical components.
4. Cooling System Maintenance
The cooling system is vital in preventing the laser source from overheating. Ensuring that the coolant levels are adequate and that the cooling system is functioning correctly prevents overheating and extends the machine’s lifespan.
II. Proper Usage Techniques
In addition to regular maintenance, employing proper usage techniques is essential in extending the lifespan of a laser cutting machine. Here are some best practices:
1. Correct Material Handling
Always use materials that are compatible with your laser cutting machine. Using inappropriate materials can cause damage to the laser source and other components. Furthermore, ensure that materials are free from contaminants that could affect the cutting process.
2. Optimal Machine Settings
Using the correct machine settings for different materials and thicknesses is crucial. Overdriving the laser or using incorrect settings can lead to excessive wear and tear on the machine. Always refer to the manufacturer’s guidelines for recommended settings.
3. Avoid Overuse
While laser cutting machines are designed for high productivity, excessive use without breaks can lead to overheating and accelerated wear. Implementing regular breaks and cooling periods during intensive operations helps maintain optimal machine performance.
4. Proper Shutdown Procedures
Always follow the manufacturer’s recommended shutdown procedures. This includes properly cooling down the laser source and other critical components before turning off the machine. Abrupt shutdowns can lead to thermal stress and damage.
III. Environmental Conditions
Furthermore, the environment in which a laser cutting machine operates plays a significant role in its longevity. Maintaining suitable environmental conditions helps prevent premature wear and damage.
1. Temperature Control
Extreme temperatures can adversely affect the performance and lifespan of a laser cutting machine. Ensure that the operating environment maintains a stable temperature within the manufacturer’s recommended range. This helps prevent overheating and ensures optimal performance.
2. Humidity Control
High humidity levels can lead to condensation, which can damage the machine’s electronics and optics. Maintaining a controlled humidity level in the operating environment is essential to prevent such issues.
3. Clean Environment
A clean and dust-free environment is crucial for the longevity of a laser cutting machine. Dust and debris can accumulate on sensitive components, leading to reduced performance and potential damage. Implementing dust control measures and regular cleaning of the work area helps maintain a clean environment.
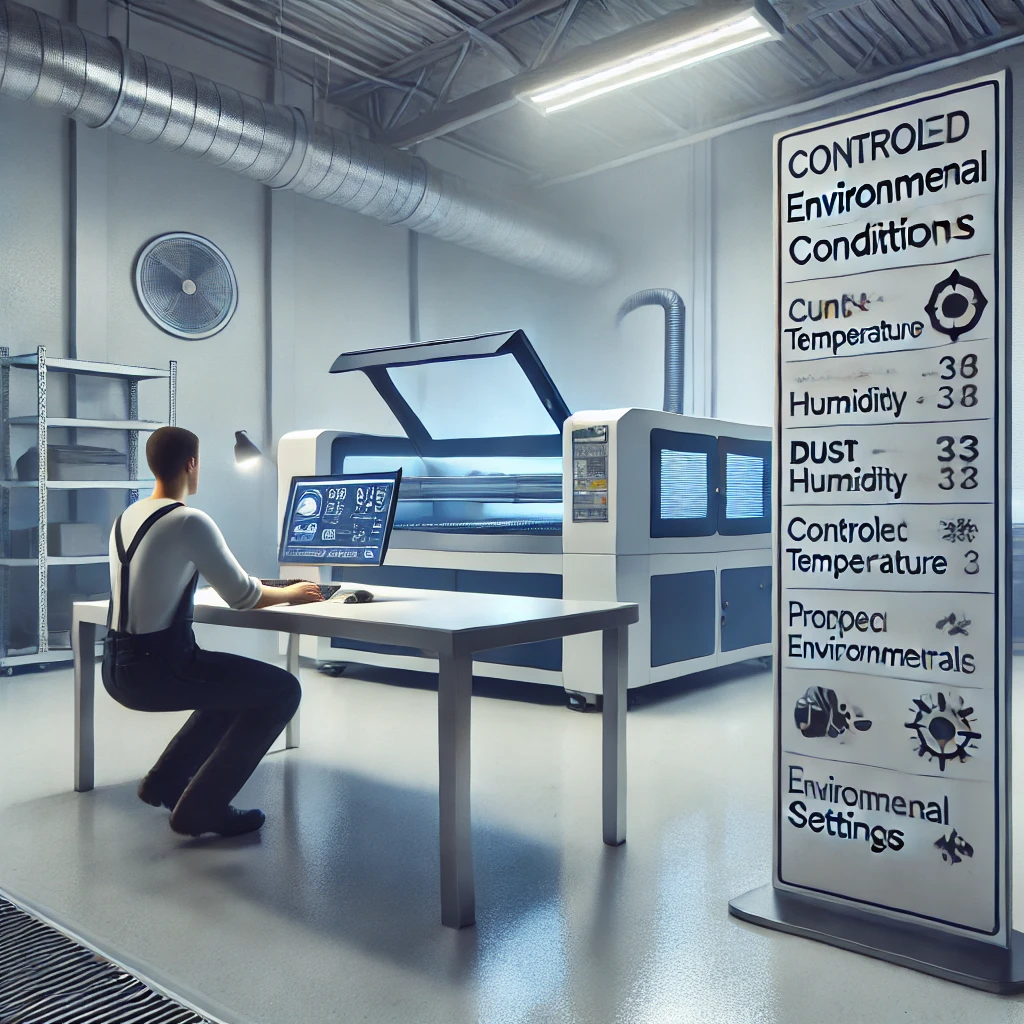
IV. Training and Skill Development
Moreover, investing in proper training and skill development for operators can significantly extend the lifespan of a laser cutting machine. Well-trained operators are more likely to use the machine correctly, perform regular maintenance, and identify potential issues before they become serious problems.
1. Operator Training
Ensure that all operators receive comprehensive training on the machine’s operation, maintenance, and safety procedures. This training should cover the correct handling of materials, machine settings, and emergency procedures.
2. Continuous Education
Encourage operators to stay updated with the latest advancements in laser cutting technology and best practices. Continuous education helps operators improve their skills and adapt to new techniques that can enhance machine performance and longevity.
3. Regular Inspections
Implement a schedule for regular inspections conducted by trained personnel. These inspections can identify early signs of wear or damage, allowing for timely interventions that prevent further deterioration.
V. Conclusion
In conclusion, extending the lifespan of a laser cutting machine involves a combination of regular maintenance, proper usage techniques, suitable environmental conditions, and operator training. By adhering to these best practices, manufacturers can ensure that their laser cutting machines remain reliable, efficient, and productive over the long term. As technology continues to evolve, staying informed and proactive in maintaining these valuable tools will remain essential for achieving sustained success in the manufacturing and production industries.