Precision is paramount in the world of laser cutting. Whether you’re working with metals, plastics, or other materials, achieving high levels of accuracy can significantly impact the quality of your work and the efficiency of your operations. Enhancing the cutting precision of your laser cutting machine involves understanding the factors that affect accuracy and implementing best practices. This comprehensive guide provides valuable insights into improving the precision of your laser cutting machine.
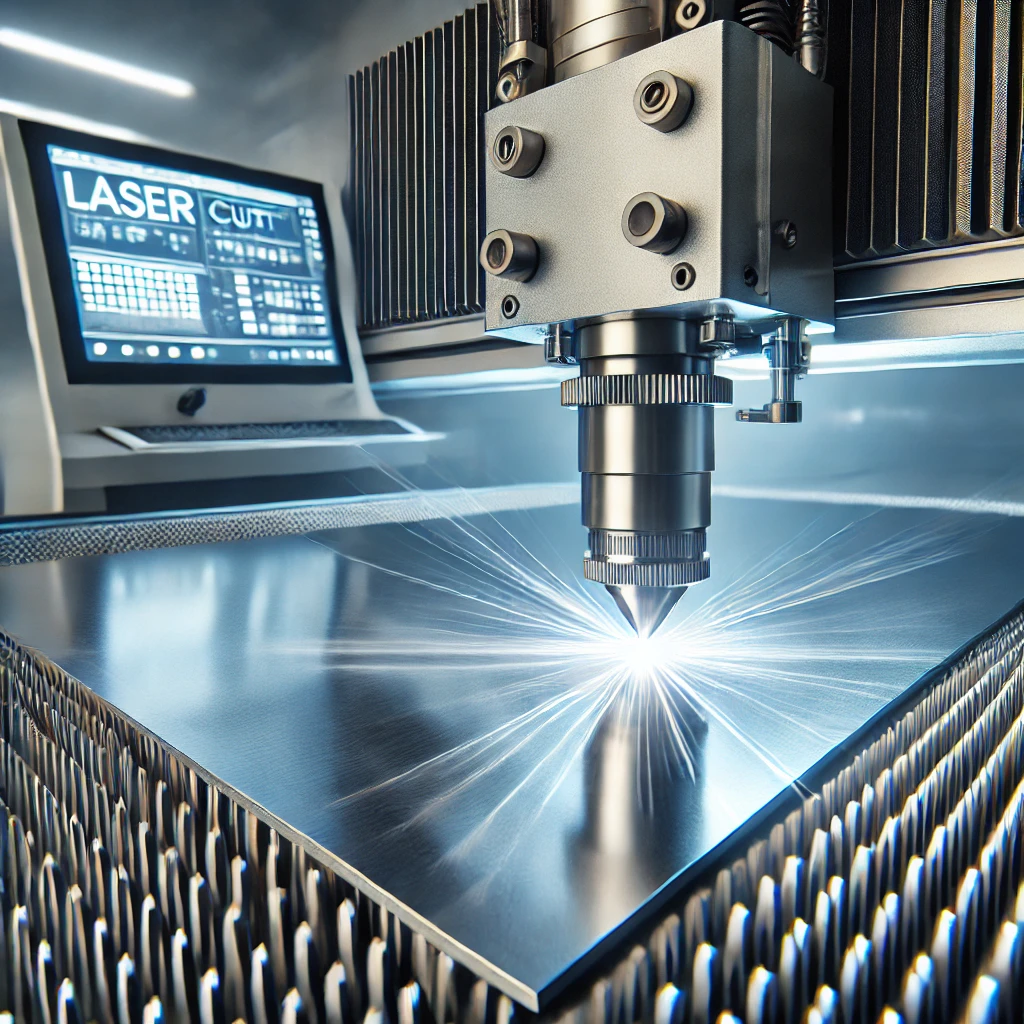
I. Understand the Factors Affecting Precision
Several factors influence the cutting precision of a laser cutting machine. These include:
1. Laser Power
The strength of the laser beam affects the cut’s sharpness and cleanliness.
2. Focus of the Laser Beam
Proper focus ensures that the laser beam cuts at the optimal point.
3. Material Type and Thickness
Different materials and thicknesses react differently to laser cutting.
4. Machine Calibration
Properly calibrated machines maintain consistent performance.
5. Environmental Conditions
Temperature, humidity, and cleanliness can impact precision.
6. Operator Skill
The expertise of the machine operator plays a crucial role.
II. Regular Maintenance and Calibration
Regular maintenance and calibration of your laser cutting machine are critical for maintaining precision. This involves:
1. Cleaning Optics
Ensure that the lenses and mirrors are clean. Dirt and debris can scatter the laser beam, reducing precision.
2. Checking Alignment
Regularly check and adjust the alignment of the laser beam to ensure it is perfectly aligned with the cutting path.
3. Replacing Worn Parts
Parts such as nozzles and lenses wear out over time and should be replaced to maintain optimal performance.
4. Software Updates
Keep the machine’s software updated to benefit from the latest improvements and bug fixes.
III. Optimize Laser Settings
Fine-tuning the laser settings can have a significant impact on cutting precision. Key settings to consider include:
1. Power Settings
Adjust the laser power to suit the material being cut. Too much power can burn the material, while too little can result in incomplete cuts.
2. Speed Settings
Slower speeds can improve precision but might reduce productivity. Find a balance that maintains accuracy without sacrificing too much speed.
3. Focus Position
The focal point of the laser should be at the optimal position for the material thickness. Use focus adjustment tools to achieve the correct focus.
4. Pulse Frequency
Adjusting the pulse frequency can improve the quality of the cut, especially for thicker materials.
IV. Use Quality Materials
The quality of the materials used can significantly affect the precision of laser cutting. High-quality, consistent materials produce more accurate cuts. Variations in material composition, thickness, or surface finish can lead to inconsistent results. Always source materials from reputable suppliers to ensure consistency.
V. Implement Advanced Cutting Techniques
Adopting advanced cutting techniques can enhance precision:
1. Assist Gas
Using assist gases like oxygen or nitrogen can improve cut quality by blowing away molten material and preventing oxidation.
2. Kerf Compensation
Adjust for the width of the cut (kerf) in your design files to ensure the finished dimensions are accurate.
3. Lead-in and Lead-out Paths
Incorporate lead-in and lead-out paths in your cutting design to improve the quality of cut starts and ends.
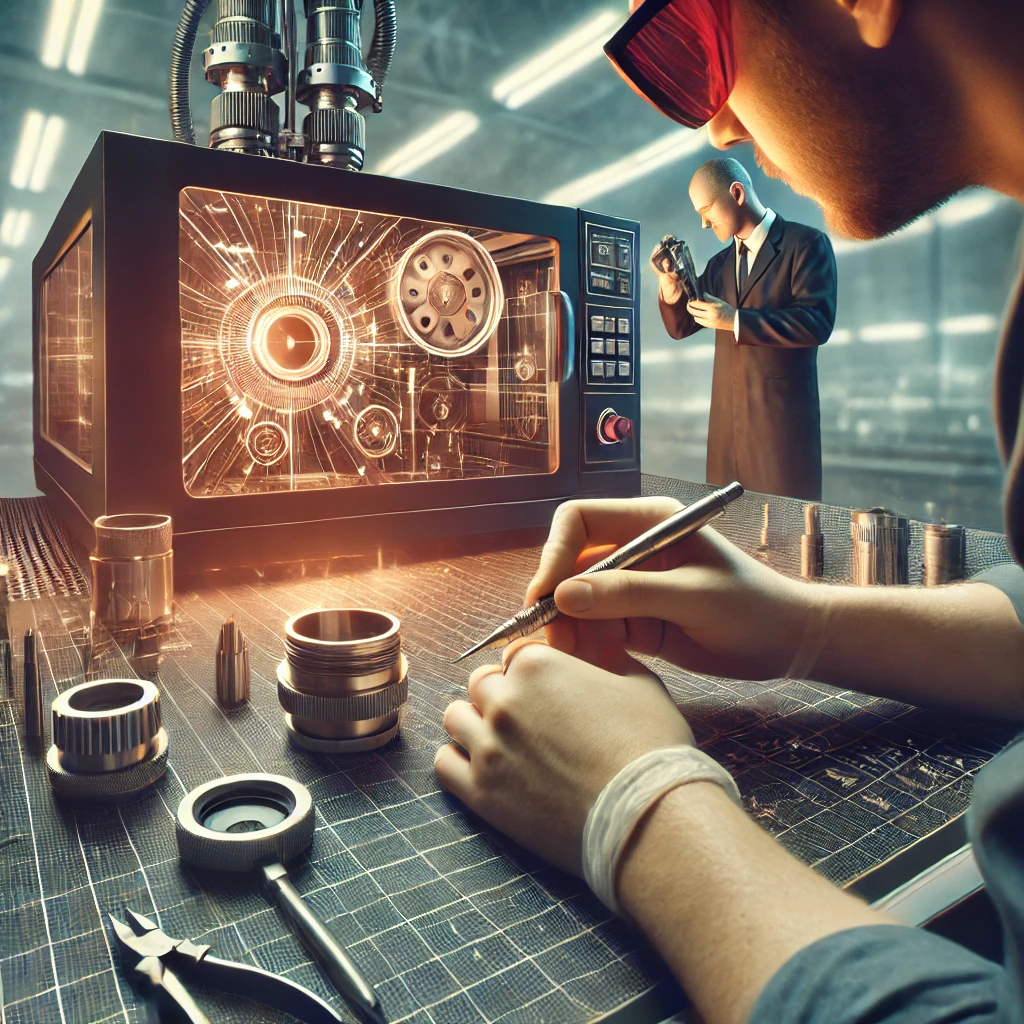
VI. Invest in Training
Operator skill is a critical factor in achieving high precision. Invest in regular training for your operators to ensure they are knowledgeable about:
1. Machine Operation
Understanding how to properly operate and adjust the machine settings.
2. Material Characteristics
Knowing how different materials react to laser cutting and how to adjust settings accordingly.
3. Maintenance Practices
Proper maintenance procedures to keep the machine in optimal condition.
VII. Monitor Environmental Conditions
The environment in which the laser cutting machine operates can impact precision. Factors to consider include:
1. Temperature and Humidity
Maintain a stable temperature and humidity level in the workspace. Extreme variations can affect the machine’s performance.
2. Cleanliness
Keep the cutting area and the machine itself clean to prevent dust and debris from affecting the laser beam.
3. Vibration
Minimize vibration in the workspace as it can cause the laser beam to wobble, affecting precision.
VIII. Leverage Technology and Automation
Utilize technology and automation to enhance precision:
1. CNC Controls
Computer Numerical Control (CNC) systems can provide precise control over the cutting process.
2. Monitoring Systems
Use monitoring systems to track the machine’s performance and detect issues early.
3. Automation
Automating certain aspects of the cutting process can reduce human error and improve consistency.
IX. Conclusion
Enhancing the cutting precision of your laser cutting machines involve a multifaceted approach, focusing on machine maintenance, optimizing settings, using quality materials, and investing in operator training. By understanding and addressing the various factors that affect precision, you can achieve cleaner, more accurate cuts, improving the quality of your work and the efficiency of your operations. Regularly review and update your practices to keep up with advancements in technology and industry standards, ensuring your laser cutting processes remain at the forefront of precision and performance.