Multi-layer laser cutting offers new possibilities in material processing. It allows manufacturers to cut through several layers of different materials in one go. This technique improves efficiency and reduces overall production time. Whether using a small metal laser cutter or larger laser cutting machines, mastering multi-layer cutting can lead to significant advancements. In this article, we explore the methods, benefits, and best practices for successful multi-layer laser cutting.
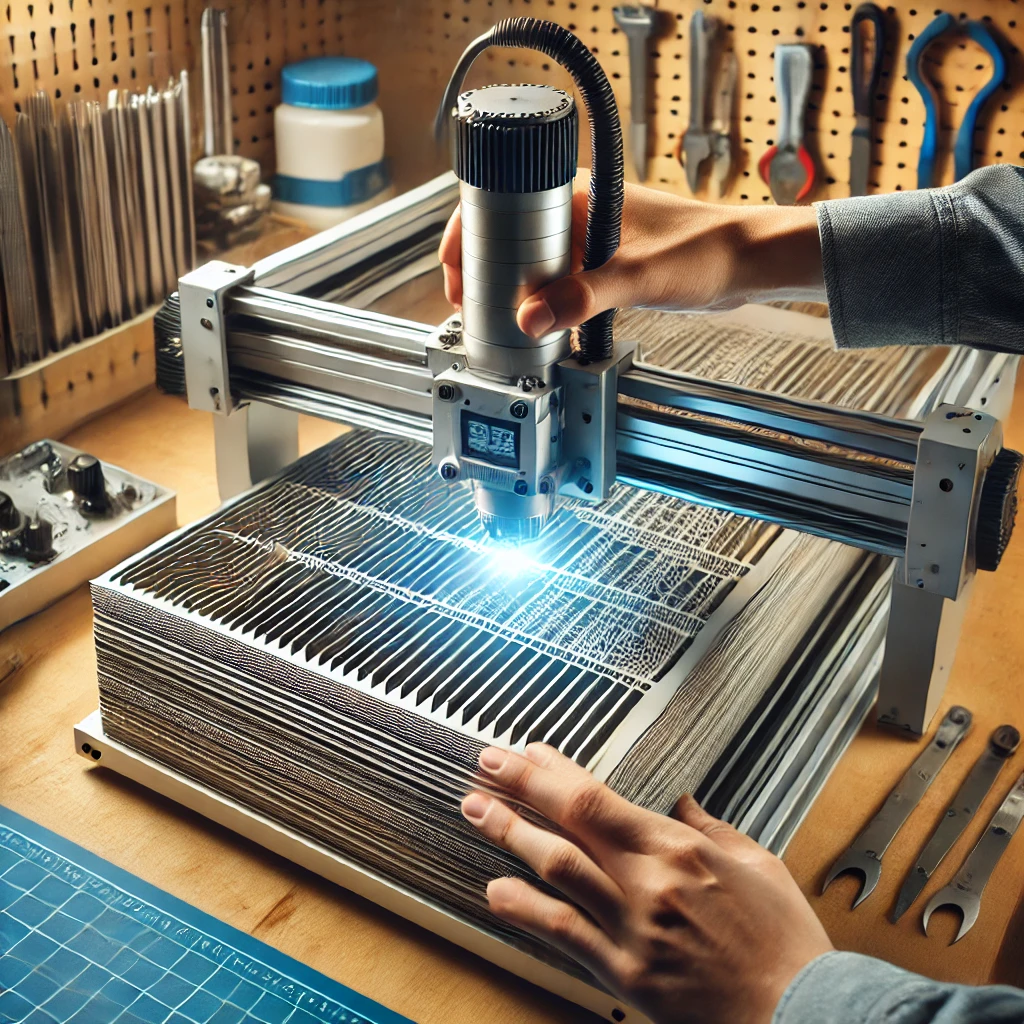
I. Understanding Multi-Layer Laser Cutting
Multi-layer laser cutting involves cutting through multiple layers of material simultaneously. This technique is especially useful for composite materials, where different layers require different settings. With a small metal laser cutter, precise control over power and speed is essential. The process ensures all layers are cut cleanly without damaging surrounding materials. Different laser cutting machines can handle this technique based on their capabilities.
II. The Importance of Layer Control
Each material layer has unique properties. This makes it necessary to adjust the laser settings for each layer. For example, metal layers require more power than plastic or fabric. By using laser cutting machines with adjustable power settings, you can cut through multiple layers efficiently. Precision is key, especially when using a small metal laser cutter. The ability to fine-tune the settings allows clean cuts across different materials.
III. Material Compatibility in Multi-Layer Cutting
Not all materials are suitable for multi-layer laser cutting. For successful results, choose materials that can withstand laser heat. Metals, plastics, and fabrics are often ideal candidates. However, when using a small metal laser cutter, ensure the power is sufficient for cutting through tougher materials. Some laser cutting machines are designed to handle a wide range of materials, making them more versatile for multi-layer projects.
IV. Benefits of Multi-Layer Cutting
Multi-layer cutting offers several benefits. First, it significantly reduces production time. By cutting multiple layers at once, manufacturers can complete tasks faster. Additionally, this technique improves material efficiency. Since the laser only passes over the material once, it minimizes waste. Whether you’re using a small metal laser cutter for intricate designs or laser cutting machines for large-scale production, the benefits of multi-layer cutting are clear.
V. Challenges in Multi-Layer Cutting
Despite its benefits, multi-layer cutting presents challenges. Different materials may react differently to the laser. Some layers may burn or melt before the laser reaches the lower layers. This can cause damage to the material. However, by adjusting the settings on laser cutting machines, you can minimize these risks. With a small metal laser cutter, regularly monitor the process to ensure all layers are cut evenly.
VI. Optimizing Laser Settings for Multi-Layer Cutting
The key to successful multi-layer cutting lies in optimizing laser settings. Power, speed, and focus are the three primary factors. For each material, adjust the power to avoid overheating. Too much power can burn through upper layers. Meanwhile, speed adjustments help control how quickly the laser moves through the layers. Laser cutting machines often come with built-in software for setting optimization. A small metal laser cutter allows for more precise adjustments, especially for intricate projects.
VII. Importance of Focus in Multi-Layer Cutting
Maintaining laser focus is critical for cutting through all layers efficiently. Poor focus can result in incomplete cuts or damaged materials. To optimize the focus, adjust the laser’s focal point based on the thickness of each layer. When using a small metal laser cutter, pay close attention to the focal distance. This ensures the laser penetrates all layers without causing uneven cuts. Many laser cutting machines feature automatic focus adjustments for ease of use.
VIII. Techniques for Reducing Heat Damage
Heat damage is a common issue in multi-layer cutting. Excessive heat can warp or melt sensitive materials. To reduce heat damage, increase the cutting speed slightly. This helps move the laser quickly through each layer, minimizing heat buildup. Another solution is using a small metal laser cutter with precise control over power and speed. Laser cutting machines equipped with cooling systems can also prevent overheating during extended cutting sessions.
IX. Applications of Multi-Layer Cutting
Multi-layer cutting has diverse applications across various industries. In automotive manufacturing, it is used to cut through layered composites. The aerospace industry benefits from cutting multiple layers of lightweight materials for structural components. Even fashion designers use multi-layer cutting to create intricate fabric designs. Whether using a small metal laser cutter for delicate projects or laser cutting machines for industrial purposes, the applications are endless.
X. Choosing the Right Laser Cutter for Multi-Layer Cutting
Selecting the right equipment is crucial for successful multi-layer cutting. If your project involves small, detailed work, a small metal laser cutter is ideal. These machines provide precision and control. However, for larger, more complex projects, consider investing in high-power laser cutting machines. These machines handle a wider range of materials and offer faster production times. It’s important to assess your needs and choose the machine that best fits your workflow.
XI. Safety Considerations in Multi-Layer Cutting
Safety is always a priority in laser cutting. Multi-layer cutting involves different materials, each with its own safety requirements. Ensure proper ventilation to avoid the buildup of harmful fumes. When using a small metal laser cutter, always wear protective gear, especially when working with metals. Larger laser cutting machines should come with built-in safety features, such as automatic shut-off and enclosed workspaces, to protect operators during cutting.
XII. Future Trends in Multi-Layer Laser Cutting
As technology advances, so will the capabilities of multi-layer laser cutting. We can expect laser cutting machines to become even more precise and efficient. Innovations in laser technology will allow for greater control over material properties. The integration of AI and machine learning could enable automatic adjustments to laser settings, further optimizing the cutting process. Small metal laser cutters will likely become more powerful, offering industrial-level capabilities in a compact form.
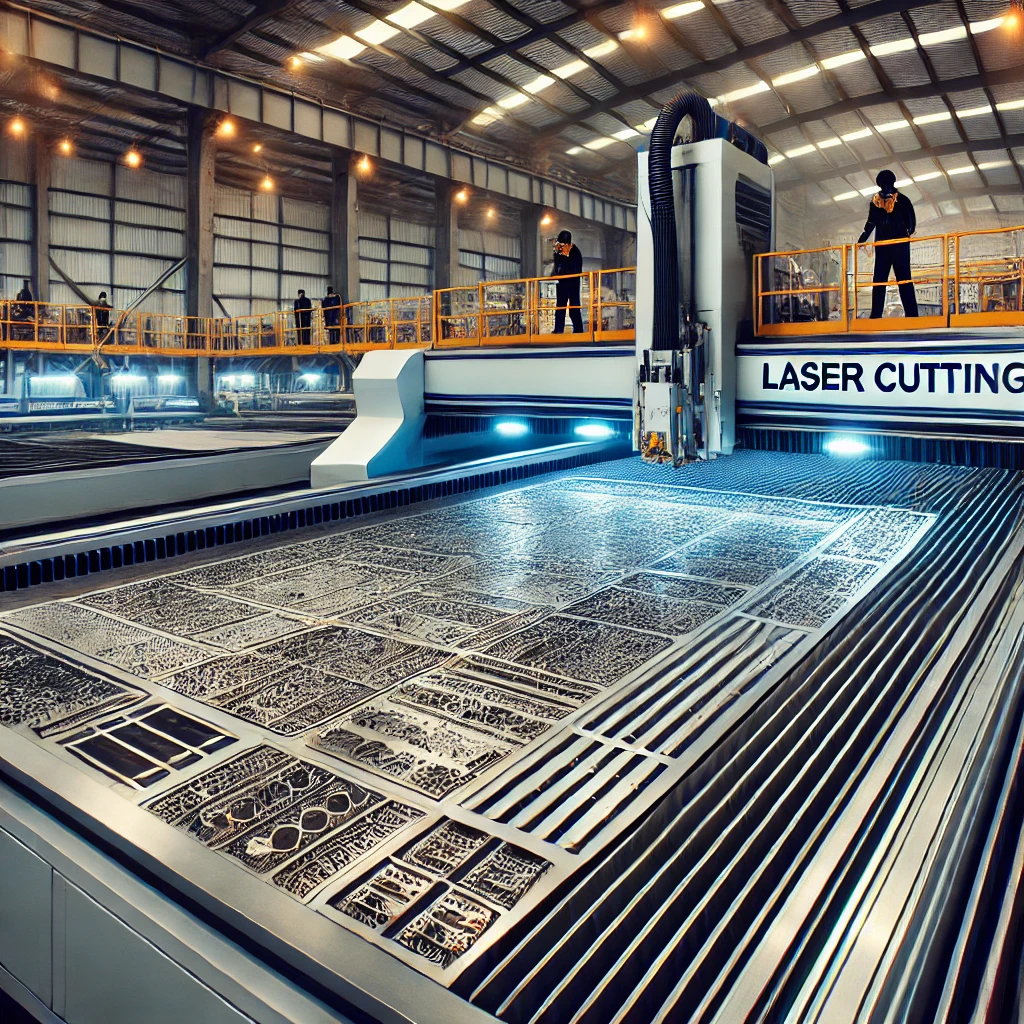
XIII. Conclusion
Multi-layer laser cutting offers an innovative approach to material processing. By cutting multiple layers at once, it improves efficiency and reduces production time. Whether using a small metal laser cutter or high-power laser cutting machines, mastering this technique can bring significant benefits. By optimizing laser settings, maintaining focus, and selecting the right materials, you can achieve clean, precise cuts across multiple layers. As technology continues to evolve, multi-layer laser cutting will open new doors for advanced manufacturing and design.