Detailed Analysis of the Working Principles of Laser Cutting Machines
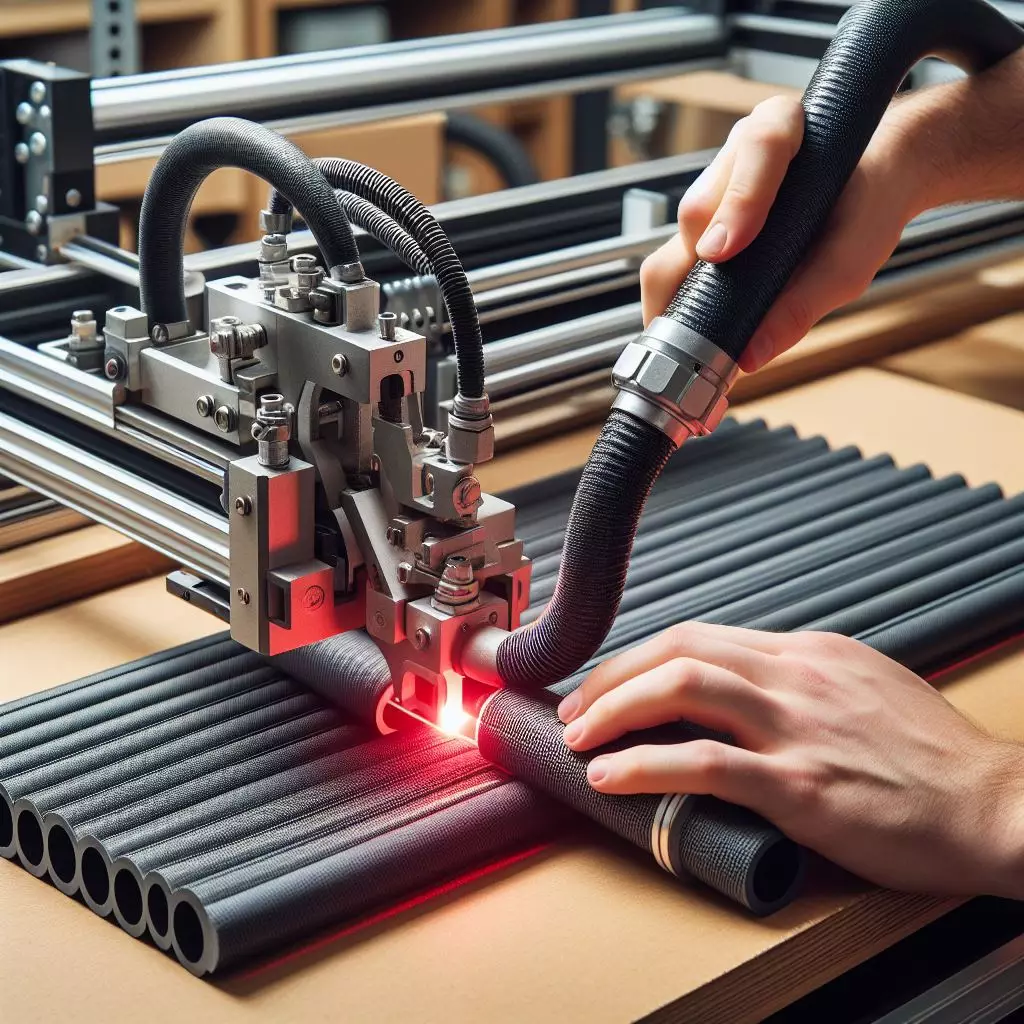
Laser cutting machines have revolutionized manufacturing processes across various industries, offering precise and efficient cutting capabilities for a wide range of materials. Understanding the intricate working principles of laser cutting machines is essential for maximizing their performance and achieving desired outcomes. This comprehensive article provides a detailed analysis of the working principles of laser cutting machines, exploring the underlying physics, components, and processes involved in their operation.
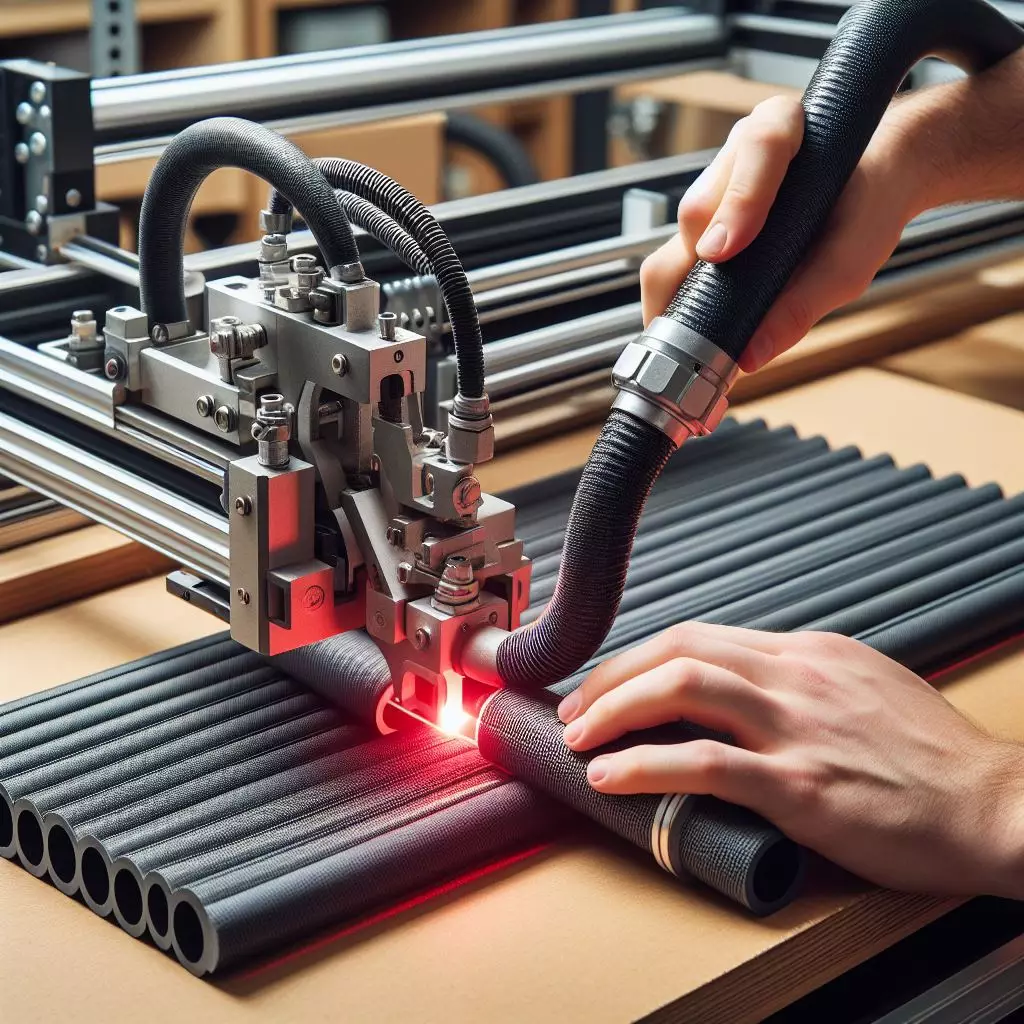
Ⅰ.Overview of Laser Cutting Technology
Laser cutting technology utilizes a highly focused laser beam to precisely cut through materials, ranging from metals and plastics to textiles and ceramics. The fundamental principle behind laser cutting involves the conversion of electrical energy into concentrated light energy, which is then directed onto the material surface to create a controlled thermal reaction. Laser cutting machines are widely used in industries such as automotive, aerospace, electronics, and manufacturing due to their versatility, accuracy, and efficiency.
Ⅱ.Fundamental Physics of Laser Cutting
Laser Generation
Laser cutting machines utilize various types of lasers, including CO2, fiber, and Nd:YAG lasers, each with distinct characteristics and applications. The laser beam is generated through a process called stimulated emission, where atoms or molecules are excited to emit photons of light.
Beam Focusing
The laser beam is focused using a series of mirrors and lenses to achieve a high-energy density spot at the material surface. Focusing the laser beam increases its intensity, allowing for precise material removal through melting, vaporization, or ablation.
Material Interaction
When the focused laser beam interacts with the material surface, it generates heat, causing localized melting or vaporization. The material is removed through a combination of thermal processes, including conduction, convection, and radiation.
Ⅲ.Components of Laser Cutting Machines
Laser Source
The laser source provides the primary energy output for the cutting process, typically in the form of a continuous or pulsed laser beam. Different types of lasers offer varying levels of power, wavelength, and beam quality to suit specific cutting requirements.
Optics System
The optics system comprises mirrors, lenses, and beam delivery components that manipulate and focus the laser beam onto the material surface. Precise control of the laser beam’s trajectory and intensity is crucial for achieving accurate cuts.
Motion Control System
The motion control system consists of servo motors, drive systems, and controllers that move the laser cutting head along the desired cutting path. High-speed and high-precision motion control is essential for achieving intricate cuts and complex shapes.
Assist Gas System
An assist gas, such as oxygen, nitrogen, or air, is used to blow away molten material from the cutting kerf and to prevent excessive heat buildup. The choice of assist gas depends on the material being cut and the desired cut quality.
Ⅳ.Laser Cutting Processes
a. Fusion Cutting: Fusion cutting involves melting the material along the cut line using a high-energy laser beam. The molten material is expelled from the kerf by the assist gas, resulting in a clean cut with minimal heat-affected zone.
b. Vaporization Cutting: Vaporization cutting, also known as ablative cutting, involves vaporizing the material directly into a gas phase using the laser beam. This process is used for cutting highly reflective materials or when precision and minimal heat input are required.
c. Flame Cutting: Flame cutting is a thermal cutting process that uses a laser beam to preheat the material surface, followed by an assist gas to create a chemical reaction that accelerates the cutting process. This process is commonly used for cutting thick materials or materials with high thermal conductivity.
Ⅴ.Factors Affecting Laser Cutting Performance
a. Material Type and Thickness: Different materials exhibit varying responses to laser cutting, with factors such as thermal conductivity, reflectivity, and absorption affecting the cutting process. Material thickness also influences cutting parameters such as laser power, cutting speed, and assist gas pressure.
b. Laser Parameters: Laser parameters, including power, wavelength, pulse duration, and focal length, determine the energy density and intensity of the laser beam. Proper selection and optimization of laser parameters are critical for achieving efficient and high-quality cuts.
c. Cutting Speed and Acceleration: Cutting speed and acceleration affect the heat input and material removal rate, impacting cut quality and process efficiency. Balancing cutting speed with other parameters is essential to optimize cutting performance while minimizing thermal distortion.
d. Assist Gas Selection: The choice of assist gas and its flow rate influence the efficiency of material removal, kerf width, and edge quality. Proper selection of assist gas parameters is crucial for achieving clean cuts and minimizing post-processing requirements.
Ⅵ.Applications and Advancements
Laser cutting machines find extensive applications in various industries, including automotive, aerospace, electronics, medical, and signage. Recent advancements in laser cutting technology include the development of hybrid laser cutting systems, integration with automation and robotics, and improvements in beam quality and control.
Conclusion
Understanding the intricate working principles of laser cutting machines is essential for optimizing their performance and achieving desired cutting results across various materials and applications. By delving into the fundamental physics, components, processes, and factors affecting laser cutting performance, manufacturers and operators can make informed decisions regarding machine selection, parameter optimization, and process optimization. Continued research and innovation in laser cutting technology promise to further enhance the capabilities and versatility of these advanced cutting systems in the future.