Fiber laser cutters are one of the important processes in modern manufacturing, especially in the field of metal processing. However, in actual operation, the laser cutting process may encounter various problems, which not only affect the processing efficiency, but also may reduce the quality of the processed parts. This article will discuss in detail several common problems and solutions in the process of laser cutting carbon steel, aiming to help operators better cope with the challenges in actual production and improve cutting quality and efficiency.
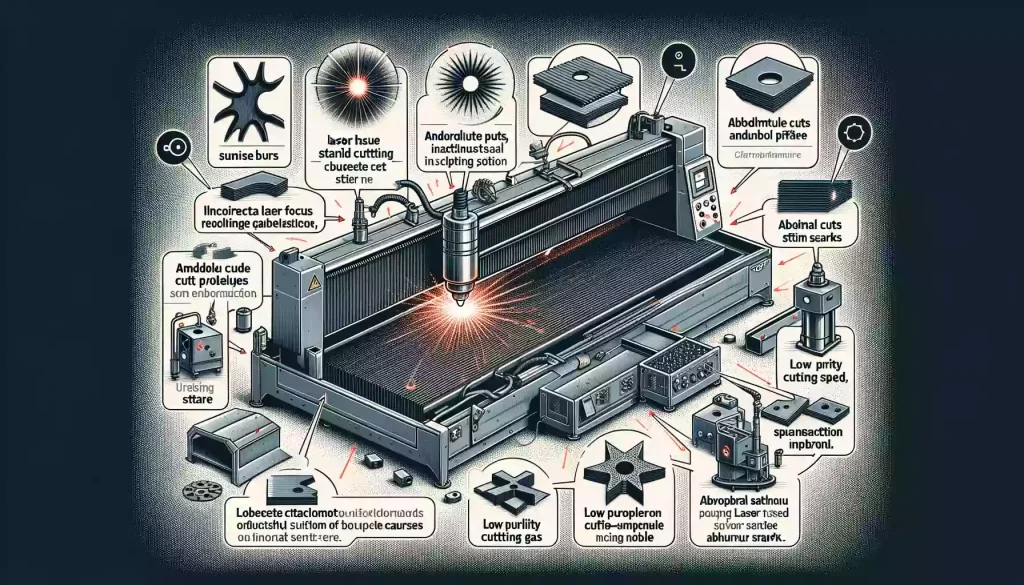
Ⅰ.Reasons for burrs on processed parts when laser cutting carbon steel
1. The laser focus position is offset:
The offset of the focus position will cause uneven cutting, resulting in burrs. The focus position test can be performed and adjusted according to the offset of the laser focus to ensure that the laser focus is accurately positioned on the cutting surface.
2. The output power of the laser is not enough:
If the laser output power is insufficient, the cutting depth will be insufficient, the edge will be uneven, and burrs will be generated. It is necessary to check whether the laser generator is working properly. If it is normal, it is necessary to observe whether the output value of the laser control button is correct. If it is not correct, make corresponding adjustments.
3. The cutting line speed is too slow:
The cutting speed is too slow, which will cause overheating, melt the edge of the material, and form burrs. The operator should increase the cutting line speed appropriately according to the actual situation to ensure the smooth progress of the cutting process.
4. The purity of the cutting gas is not enough:
Low-purity cutting gas will affect the cutting effect and cause burrs. Therefore, high-quality cutting working gas should be provided to ensure the cleanliness and efficiency of the cutting process.
5. Instability caused by long machine operation time:
A fiber laser cutter tool that has been running for a long time may become unstable, affecting the cutting quality. At this time, it is necessary to shut down and restart to restore the normal working state of the machine tool.
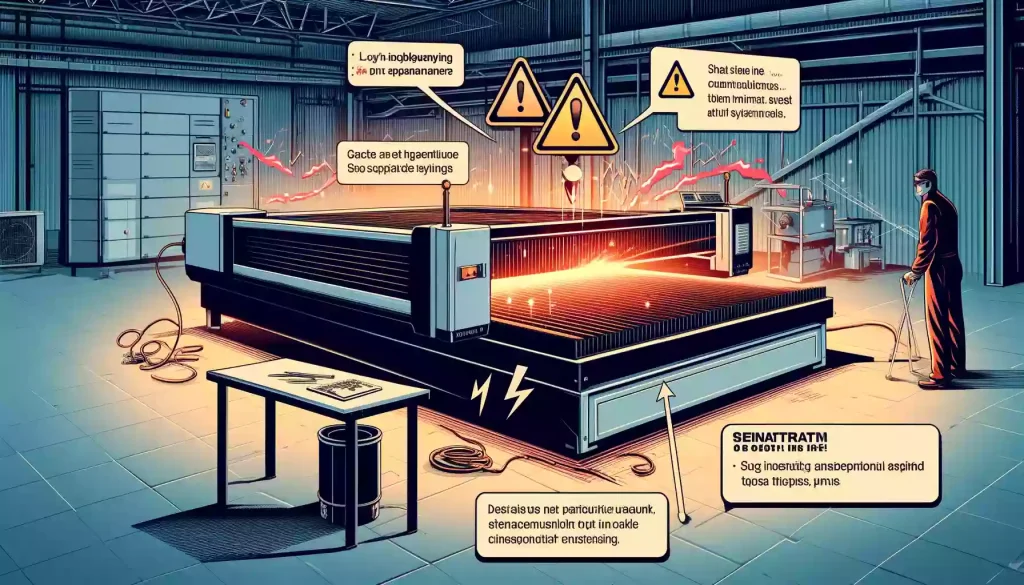
Ⅱ.Reasons for incomplete cutting during laser cutting
1. The selection of the laser nozzle does not match the thickness of the processing plate:
Unmatched nozzles will cause the laser to be unable to fully penetrate the material. It is necessary to replace the appropriate nozzle or adjust the thickness of the processing plate.
2. The laser cutting line speed is too fast:
Excessive cutting speed will prevent the laser from completely cutting the material. It is necessary to appropriately reduce the cutting line speed to ensure that the laser can fully act on the material.
Ⅲ.Reasons for abnormal sparks during laser cutting:
When cutting low-carbon steel, if abnormal sparks occur, it may affect the smoothness and processing quality of the cutting section of the workpiece. Under normal circumstances, when cutting low-carbon steel, the spark beam should be long, flat, and have fewer forks. If abnormal sparks occur, the following situations should be considered:
1. Severe wear and tear of the laser head nozzle:
Severely worn nozzles will affect the normal output of the laser, and the nozzles should be replaced in time to restore the normal cutting effect.
2. Insufficient cutting working gas pressure:
In the absence of a new nozzle to replace, you can try to increase the cutting working gas pressure to improve the cutting quality.
3. Loose threads at the connection between the nozzle and the laser head:
If the threads at the connection between the nozzle and the laser head are loose, the laser output will be unstable. You need to immediately stop cutting, check and re-tighten the threads to ensure a stable connection.
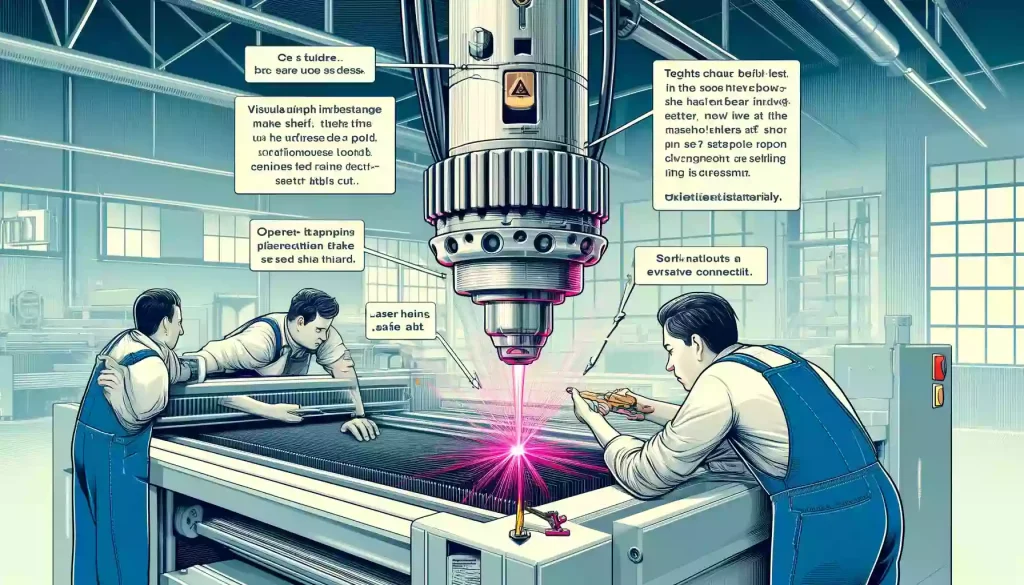
Final Thoughts
In summary, the problems of burrs, incomplete cutting, and abnormal sparks that may be encountered during laser cutting of carbon steel are mainly due to improper equipment adjustment, unreasonable cutting parameter settings, and equipment component wear and tear. By timely checking and adjusting the laser focus position, laser output power, cutting speed, and cutting gas purity, as well as regular maintenance and replacement of consumable parts, the quality and efficiency of laser cutting can be effectively improved. It is hoped that the methods and suggestions provided in this article can provide a reference for laser cutting operators and help them achieve better cutting results in actual operations.