Metal is a lustrous and ductile material, making it suitable for creating beautiful and intricate crafts or jewelry. Such as gold rings, silver necklaces, and iron artifacts. Metals initially have an absorption rate of only 0.5% to 10% for a 10.6 μm laser beam. However, when a focused laser beam with a power density exceeding 10^6 W/cm² hits the metal surface, the surface begins to melt within microseconds. The absorption rate of most metals in a molten state increases dramatically, typically rising to 60% to 80%.
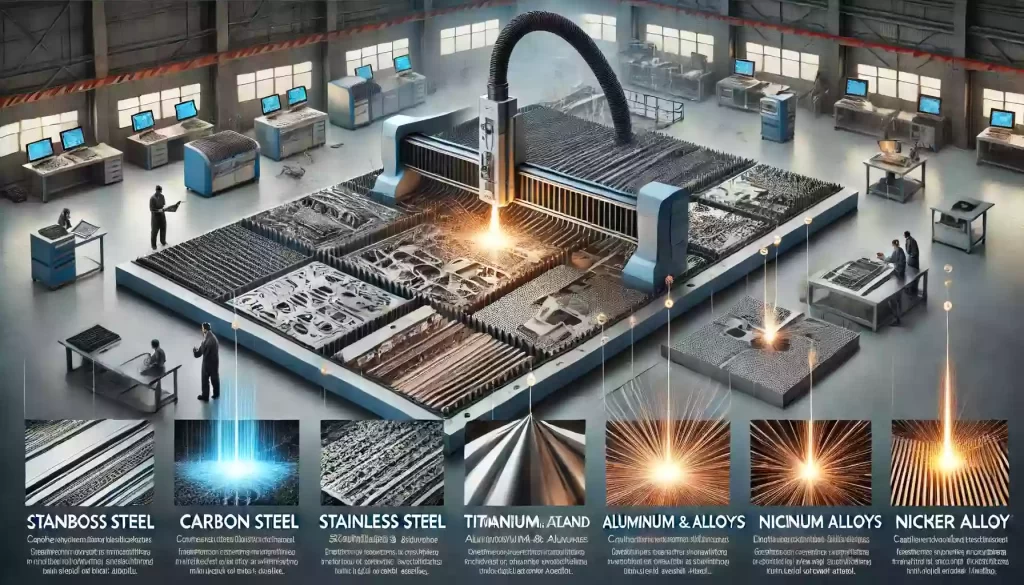
Ⅰ.Principle of laser cutting machine
Fiber laser cutter involves using a high-density laser beam to scan the material’s surface, heating it to thousands to tens of thousands of degrees Celsius in a very short time, causing the material to melt or vaporize. The molten or vaporized material is then blown away from the cutting seam by high-pressure gas, achieving the purpose of cutting. Laser cutting technology is widely used in the processing of both metallic and non-metallic materials. It significantly reduces processing time, lowers costs, and improves workpiece quality.
Ⅱ. Carbon Steel Laser Cutting Process
Modern laser cutting systems can cut carbon steel plates up to 20 mm thick. The use of an oxidation melting fiber laser cutter allows for controlling the cut width within a satisfactory range. For thin plates, the cut width can be as narrow as approximately 0.01 mm, greatly enhancing cutting precision and efficiency. For example, in the automotive industry, laser-cut carbon steel parts are used for car body frames and structural components due to their precise cuts and smooth edges. It facilitate easy assembly and welding.
Ⅲ. Stainless Steel Laser Cutting Process
Fiber laser cutting machines are highly effective tools for the manufacturing industry. By strictly controlling the heat input during the laser cutting process, the heat-affected zone of the cut edge can be minimized. This effectively preserves the excellent corrosion resistance of stainless steel, making it widely used for manufacturing precision parts. For instance, in the medical device industry, stainless steel is often used for surgical instruments and implants. It maintaining the material’s integrity and cleanliness is crucial.
Ⅳ. Titanium and Alloy Laser Cutting Process
Pure titanium can effectively couple with the thermal energy converted by the focused laser beam. When oxygen is used as the auxiliary gas, the chemical reaction is intense. This resulting in faster cutting speeds but potentially forming an oxide layer on the cut edge and risking overburning. For safety and quality assurance, using air as the auxiliary gas is preferable. Titanium alloys commonly used in the aerospace industry have good laser cutting quality. Though there may be some minor dross at the bottom of the cut, which is easy to remove.
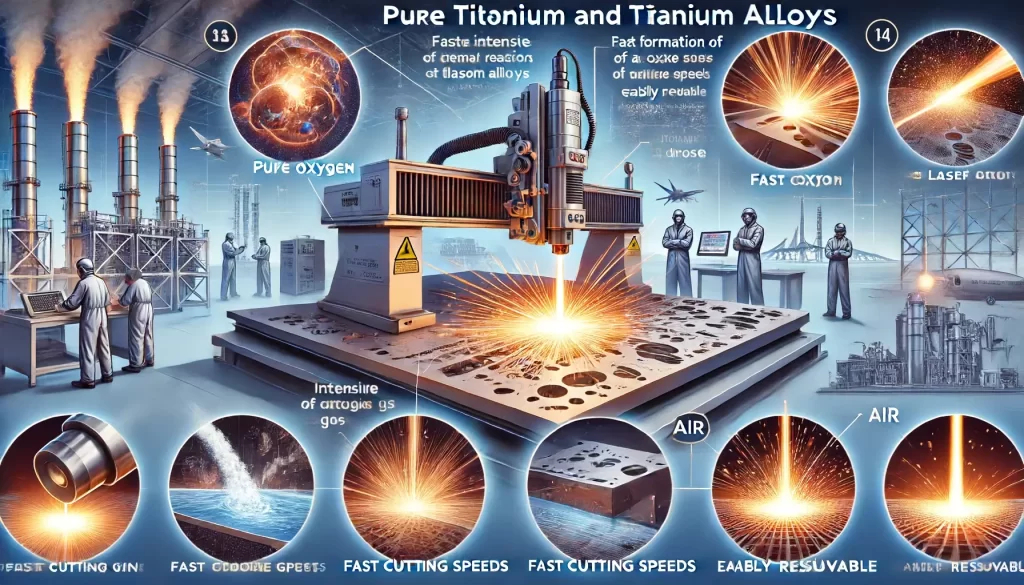
Ⅴ. Aluminum and Alloy Laser Cutting Process
Aluminum cutting is categorized as melt cutting. The auxiliary gas is primarily used to blow away the molten products from the cutting area, typically resulting in good cut surface quality. For some aluminum alloys, it is crucial to prevent the formation of intergranular microcracks on the cut surface to ensure the final product’s quality and performance. An example of aluminum laser cutting application is in the electronics industry, where aluminum casings for smartphones and laptops are laser cut to achieve high precision and smooth edges, ensuring a perfect fit and finish.
Ⅵ. Copper and Alloy Laser Cutting Process
Due to its high reflectivity, pure copper (red copper) cannot be cut with a CO2 laser beam. It requires a fiber laser cutting machine with specific high-reflectivity resistance capabilities. For brass (copper alloy), high-power laser cutting machines can be used, and air or oxygen can be used as auxiliary gases to cut thinner plates effectively. For instance, in the plumbing industry, brass fittings and valves are often laser cut to ensure precise dimensions and high-quality finishes, which are essential for leak-proof connections.
Ⅶ. Nickel Alloy Laser Cutting Process
Nickel-based alloys, also known as superalloys, come in various types, most of which can be cut using oxidation melting techniques. The laser cutting of nickel-based alloys typically achieves good cut edge quality, making them an essential material in industrial processing. An example of their application is in the power generation industry, where nickel alloys are used for turbine blades and other high-temperature components due to their ability to withstand extreme heat and stress.
Ⅷ. Alloy Steel Laser Cutting Process
Most alloy structural steels and alloy tool steels can achieve good cut edge quality using laser cutting methods. Even for high-strength materials, precise control of process parameters can result in straight, slag-free cuts. However, for tungsten-containing high-speed tool steels and hot-mold steels, issues like melting and dross formation can occur during laser cutting, requiring careful control of cutting parameters. For example, in the manufacturing of precision tools and dies, laser cutting of alloy steels ensures accurate dimensions and smooth surfaces, which are critical for the performance and longevity of the tools.
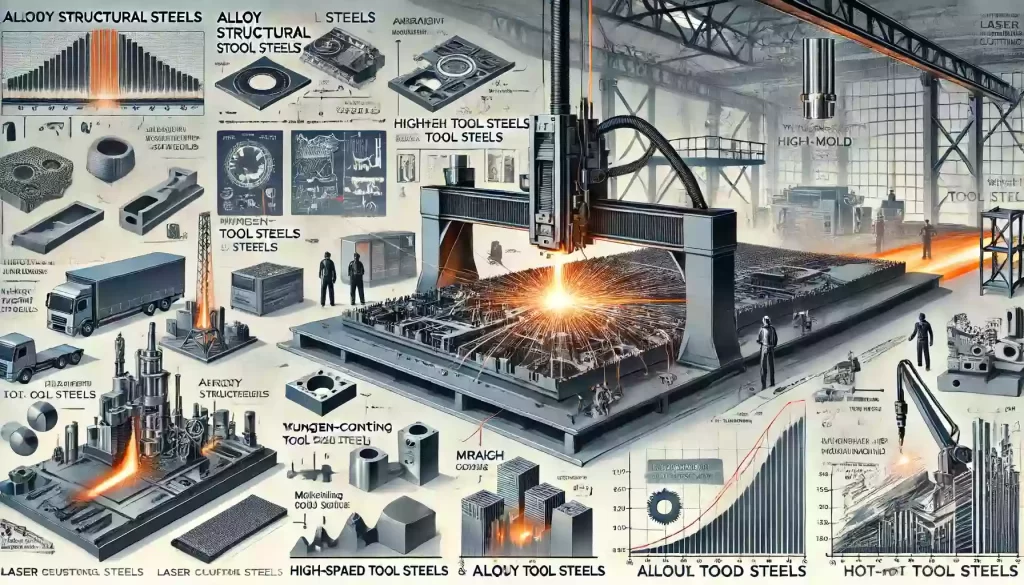
Final Thoughts
As the laser industry rapidly develops, related laser technologies and products are becoming increasingly mature. In the field of laser cutting machines, fiber laser cutting machines have a lower maintenance cost and higher cutting quality compared to YAG and CO2 laser cutting machines. This gives them a greater market share, particularly in the sheet metal processing industry. The widespread adoption of fiber laser cutting machines not only drives technological advancement in manufacturing but also provides robust support for high-precision and high-efficiency processing needs.