In modern manufacturing, cutting and stamping technologies are indispensable. The punch press, as a traditional metal processing tool, has been in use for decades. However, with the rise of laser cutting technology, its high precision, high efficiency, and wide material adaptability are making it a strong alternative to punch presses. This article will explore the reasons why fiber laser cutters are gradually replacing punch presses and their future trends in the manufacturing industry.
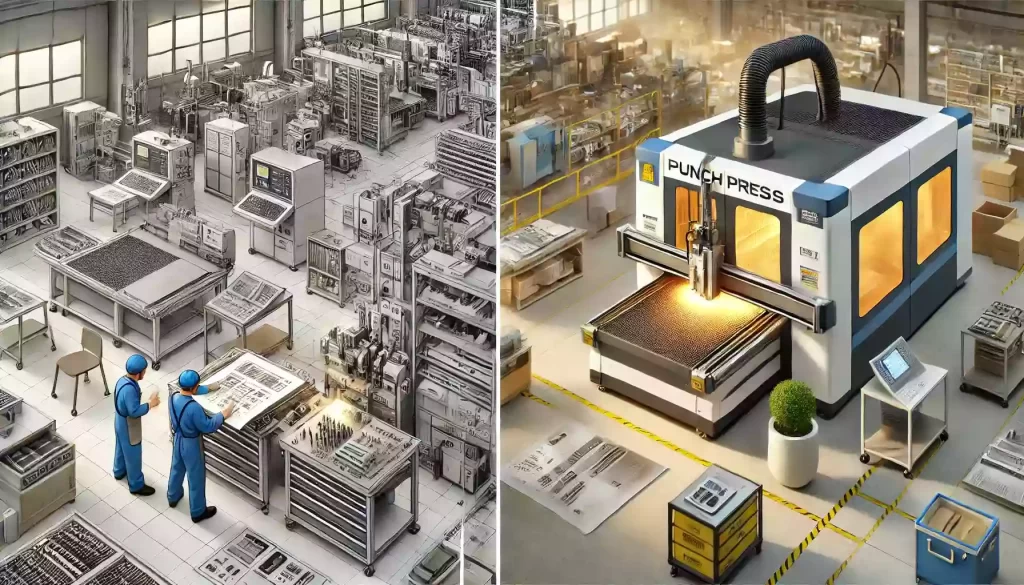
Ⅰ.Advantages of Laser Cutting Machines
1.High precision and quality:
Laser cutting machines can achieve micron-level cutting precision, far superior to traditional punch presses. This high precision not only improves product quality but also reduces the need for subsequent processing. Laser cutting provides smooth, burr-free edges, greatly enhancing the appearance and precision of the finished product.
2.High efficiency and flexibility:
Fiber laser cutters have very high cutting speeds, especially in thin sheet metal processing. They can quickly switch between different cutting tasks without the need to change molds, greatly increasing production flexibility and response speed. This is particularly important in modern manufacturing, where frequent changes in production lines are common.
3.Wide material adaptability:
Laser cutting machines can handle a variety of materials, including metals, plastics, wood, and composites. In contrast, punch presses are mainly suitable for metal materials and wear out quickly when processing high-hardness materials, increasing maintenance costs. The non-contact processing of laser cutting machines avoids mechanical stress on the material, reducing the likelihood of deformation.
4.Reduced costs and maintenance requirements:
Although the initial investment in laser cutting machines is high, their high efficiency and low maintenance requirements can significantly reduce total costs over the long term. Punch presses require frequent mold replacements and maintenance, which not only increases production costs but also affects production continuity and efficiency. The main maintenance tasks for laser cutting machines are cleaning the optical system and periodically replacing the laser source, which are relatively simple and inexpensive.
Ⅱ.Limitations of Punch Presses
1.Limitations in precision and quality:
The precision of punch presses depends mainly on the accuracy of the molds and the stability of the stamping process. As the molds wear out, the precision of stamping gradually decreases, affecting the quality of the finished product. Additionally, the stamping process easily produces burrs and deformation, requiring extra post-processing steps to correct the cut quality.
2.Lack of flexibility:
Punch presses have poor processing flexibility and require frequent mold changes for different tasks. This not only increases production time but also limits the diversity of product designs. In modern manufacturing, flexibility and quick response to market demands are crucial, and punch presses struggle to meet these requirements.
3.Material limitations:
Punch presses are primarily used for processing metal materials, performing best with high-hardness metals and thick sheets. However, they are less suitable for non-metallic materials or composites. Moreover, the molds wear out quickly when processing high-hardness materials, leading to increased production costs and downtime for replacements and maintenance.
4.Safety and environmental issues:
Punch presses require significant mechanical force during operation, increasing operational risks and the likelihood of accidents. The noise and vibration generated during stamping also negatively impact the factory environment and worker health. In contrast, laser cutting machines offer higher operational safety, lower noise, and less pollution, contributing to a safer and more environmentally friendly production environment.
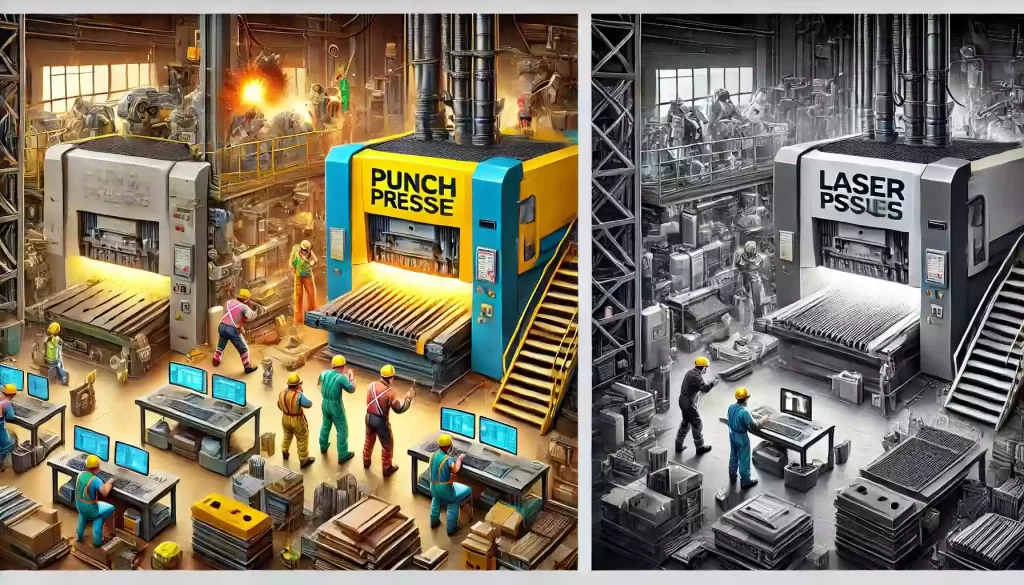
Ⅲ.Trends in Laser Cutting Machines Replacing Punch Presses
1.Technological advances driving development:
With continuous advancements in laser technology, the performance and efficiency of laser cutting machines are steadily improving. The development and application of new types of lasers, such as fiber lasers and ultrafast lasers, enable laser cutting to be applied to more materials and complex tasks. The technological progress of laser cutting allows it to surpass traditional punch presses in terms of precision, speed, and applicability.
2.Economic benefits driving adoption:
Although the initial investment in laser cutting machines is high, their efficient production capabilities and low maintenance costs can bring significant economic benefits in the long run. As laser cutting technology matures and equipment costs decrease, small and medium-sized enterprises are increasingly able to afford this investment, driving widespread adoption across various industries.
3.Environmental and safety requirements:
As environmental and safety regulations become stricter, companies are paying more attention to environmental and safety issues in production processes. The low pollution, low noise, and high safety of laser cutting machines make them more compliant with modern manufacturing’s environmental and safety standards. Against this backdrop, laser cutting machines are becoming the ideal choice to replace punch presses.
4.Digitization and intelligent trends:
Laser cutting machines integrate with modern digitization and intelligent manufacturing technologies, enabling highly automated and intelligent production processes. By incorporating advanced numerical control systems and intelligent software, laser cutting machines can achieve automated operations, adaptive adjustments, and real-time monitoring, significantly improving production efficiency and quality. This trend further accelerates the replacement of traditional punch presses by laser cutting machines.
Ⅳ.Application Cases
1.Automotive manufacturing:
In automotive manufacturing, laser cutting machines are widely used for cutting and processing body parts. Their high precision and high efficiency meet the complex shapes and high-quality requirements of automotive components while reducing mold replacement and maintenance costs, significantly improving production efficiency.
2.Electronics manufacturing:
The casings and internal structures of electronic products often require high precision and complex shapes. Laser cutting machines effectively meet these demands. Compared to traditional punch presses, laser cutting machines can complete the processing of electronic product components more quickly and accurately, enhancing product quality and production efficiency.
3.Furniture manufacturing:
In furniture manufacturing, laser cutting machines are used for cutting and engraving wood, plastic, and metal components. Laser cutting technology not only improves the processing precision and aesthetics of furniture parts but also increases design flexibility, making furniture products more competitive in the market.
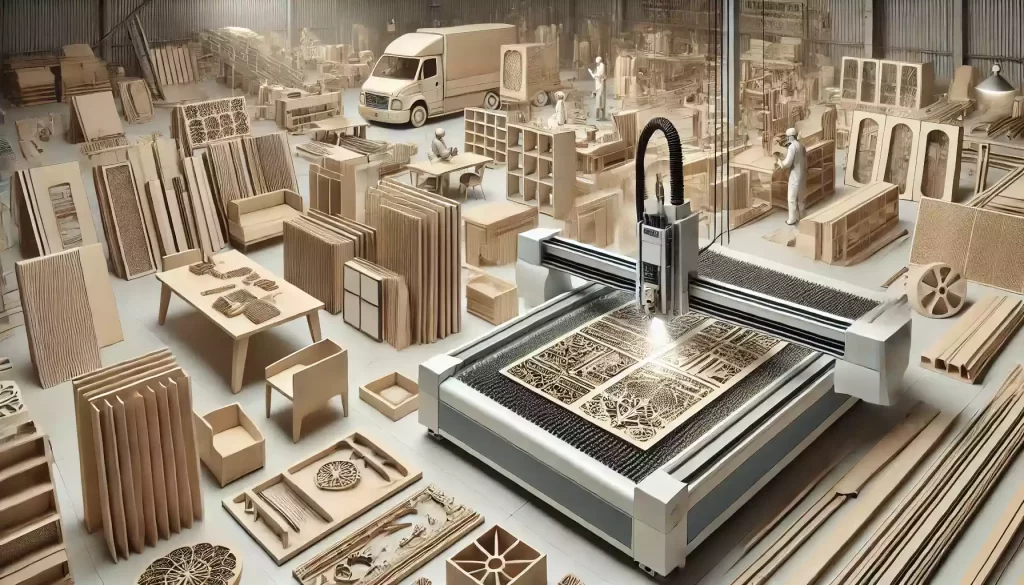
Final Thoughts
Laser cutting machines, with their high precision, high efficiency, wide material adaptability, and low maintenance requirements, are gradually replacing traditional punch presses in many manufacturing fields. With continuous technological progress and cost reduction, laser cutting machines will play an increasingly important role in future manufacturing. Companies should actively follow this trend, fully leveraging the advantages of laser cutting technology to enhance production efficiency and product quality, and meet the ever-changing market demands.