Fiber laser cutters have become indispensable in various industries due to their precision and efficiency in cutting materials. However, one common issue that operators often encounter is the sudden breakage of the cutting wire, specifically the molybdenum wire. This problem can disrupt production and lead to significant downtime and maintenance costs. Understanding the underlying causes of wire breakage is crucial for maintaining the smooth operation of laser cutting machines and ensuring high-quality output. This article delves into the primary reasons for sudden wire breakage during the laser cutting process, providing detailed insights and practical solutions to mitigate this issue.
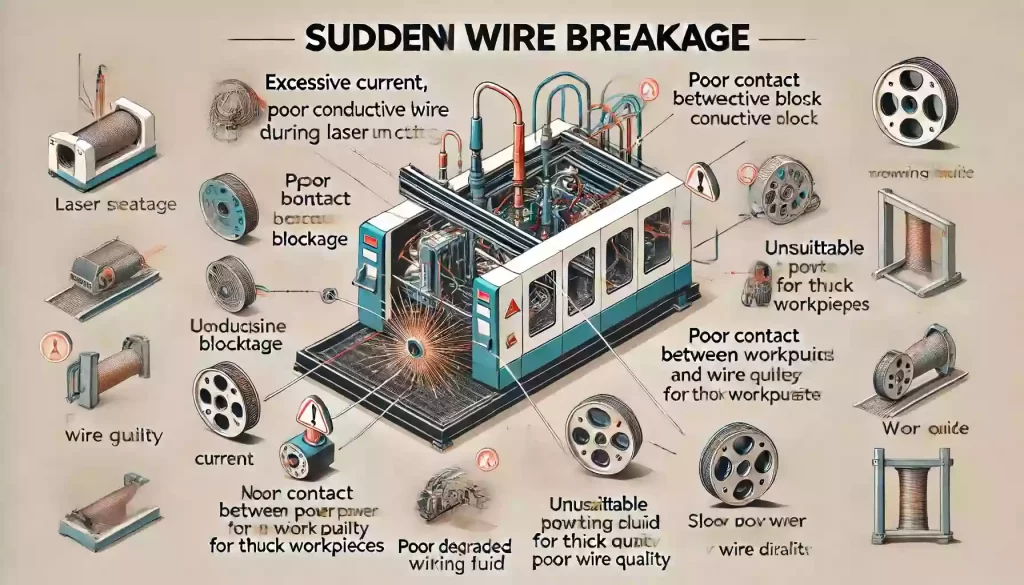
Ⅰ.Improper selection of electrical parameters and excessive current
The selection of electrical parameters is crucial during the laser cutting process. If the current is too high, the molybdenum wire will be exposed to excessive heat, causing it to heat up rapidly. This reduces its strength and durability, ultimately leading to wire breakage. Therefore, adjusting the current parameters appropriately based on the actual cutting conditions is essential to avoid damage to the wire.
Ⅱ.Improper feed rate adjustment with frequent open and short circuits:
The adjustment of the feed rate significantly impacts the stability of fiber laser cutters. If the feed rate fluctuates, it can cause instability in the cutting current, increasing the frequency of open and short circuits. This irregular stress can damage the molybdenum wire, increasing the likelihood of wire breakage. Maintaining a consistent feed rate can help mitigate this issue.
Ⅲ.Improper use of working fluid:
The working fluid used in laser cutting plays a critical role in ensuring smooth operation. Using incorrect fluids, such as regular machine tool emulsions, or using fluids that are too dilute, dirty, or have been used for too long, can negatively impact cutting quality and the lifespan of the molybdenum wire. Correct selection and maintenance of the working fluid can effectively reduce wire wear and breakage.
Ⅳ.Pipeline blockage leading to reduced working fluid flow:
Blockages in the working fluid pipeline can decrease the flow rate, affecting cooling and lubrication. This causes the molybdenum wire to work under high temperatures for extended periods, increasing the risk of wire breakage. Regularly checking and cleaning the working fluid pipelines to ensure they are clear is a necessary measure to maintain the laser cutting machine’s normal operation.
Ⅴ.Poor contact between conductive block and molybdenum wire:
Poor contact or indentations on the conductive block caused by the molybdenum wire can increase contact resistance, causing the wire to overheat during operation and eventually break. Regularly inspecting the contact condition between the conductive block and the molybdenum wire and ensuring a smooth and good contact can significantly reduce the occurrence of wire breakage.
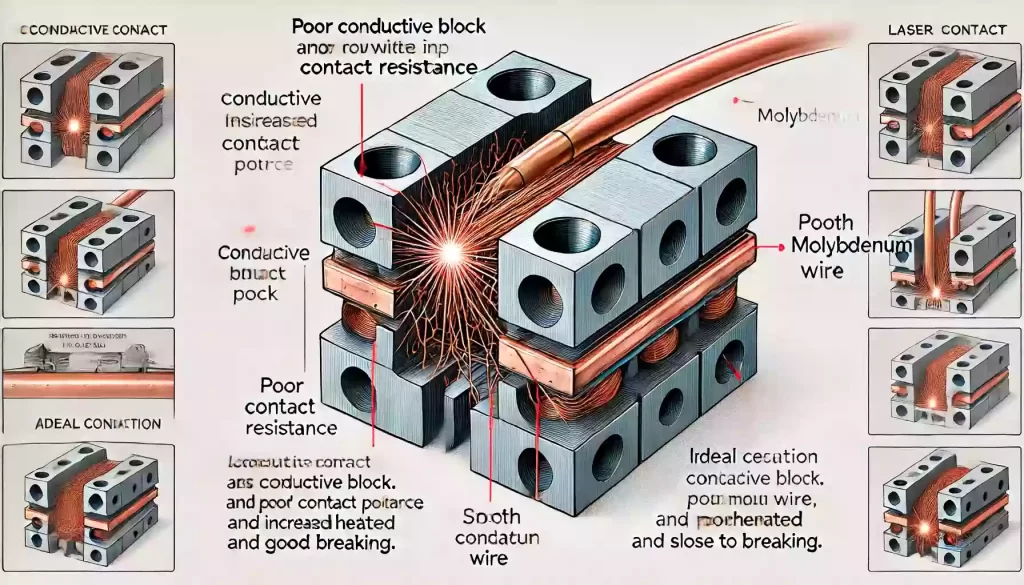
Ⅵ.Inappropriate settings for cutting thick workpieces:
When cutting thick workpieces, if the interval is set too short, the molybdenum wire will continuously work under high temperatures, leading to overheating and breaking. Additionally, using unsuitable working fluids for thick workpieces can also affect cutting performance and the wire’s lifespan. Thus, it is essential to set appropriate intervals and select suitable working fluids for cutting thick materials.
Ⅶ.Degraded performance of pulse power supply clipping diode:
If the pulse power supply’s clipping diode performance deteriorates, resulting in a large negative wave during processing, it will cause the molybdenum wire to wear out quickly in a short time, leading to wire breakage. Regular inspection and maintenance of the laser cutting machine’s power supply system to ensure its normal operation is a crucial measure to prevent wire breakage.
Ⅷ.Poor quality or improper storage of molybdenum wire:
The quality of the molybdenum wire directly affects its lifespan and cutting performance. Poor-quality wire or improper storage, leading to oxidation or damage from improper tools during installation, increases the risk of wire breakage. Choosing high-quality molybdenum wire and storing it properly is fundamental to ensuring the normal operation of the laser cutting machine.
Ⅸ.Slow rotation speed of the wire storage reel:
A slow rotation speed of the wire storage reel causes the molybdenum wire to stay in the working area for too long, increasing wear and the possibility of breakage. Ensuring an appropriate rotation speed of the wire storage reel so that the wire stays in the working area for a reasonable time can effectively reduce the occurrence of wire breakage.
Ⅹ.Incorrect diameter selection of the molybdenum wire for cutting workpieces:
When cutting different thicknesses and materials, selecting the appropriate diameter of the molybdenum wire is crucial. An incorrect wire diameter can cause excessive or insufficient stress during cutting, affecting the cutting quality and increasing the risk of wire breakage. Therefore, choosing the appropriate wire diameter based on the specific workpiece conditions is key to ensuring cutting quality and wire lifespan.
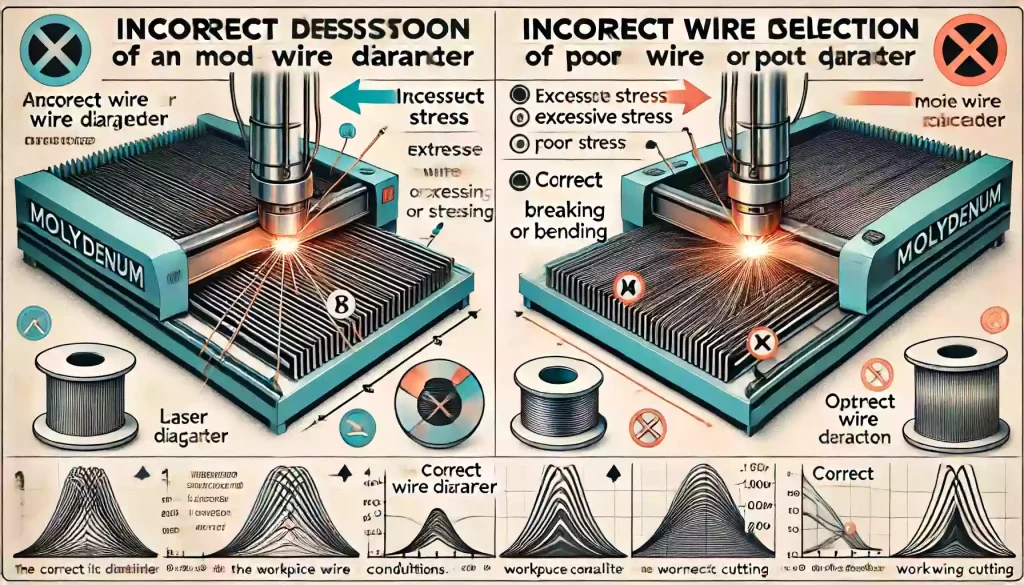
Final Thoughts
In summary, the sudden breakage of the wire during laser cutting can result from various factors, ranging from the selection of electrical parameters to the use of working fluids, maintenance of mechanical parts, and the quality of the molybdenum wire. By appropriately setting cutting parameters, regularly maintaining equipment, selecting suitable working fluids, and using high-quality molybdenum wire, the occurrence of wire breakage can be effectively reduced, thereby improving the efficiency and quality of laser cutting.